Process Costing Steps Transcript
Costing Methods > Process Costing > Process Costing Steps
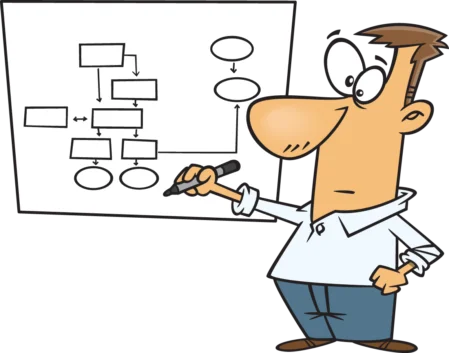
There are five steps in process costing. They are: summarize the physical flow of units; compute output in terms of the equivalent units; summarizes total costs that need to be accounted for; compute the cost per equivalent unit; and finally, assign total costs to units completed and to units in ending inventory.
This last step is the real reason we have the prior four. Without the five steps we wouldn't be able to figure out the cost of the units completed and transferred out, nor the cost of the partially completed ending inventory.
1.The first step is summarizing the physical flow of units.
In this example, WIP has 225 partially completed units from the prior period which are shown here as beginning inventory.
Additionally, 575 units were started during the period, so we need to be able to account for 800 units.
There are only two things that can happen to our units. Either they were completed and transferred out to the next process or they remain as partially completed units in ending inventory.
Either way the total needs to be 800 and you can see from here that it is.
Another way to look at this is with the WIP T account. Visually, this is what's happening. You see beginning work in process and the units started on the debit side.
The ending units are 180 and that's also on the debit side. 620 units were completed and transferred out, and that's on the credit side. Now these are just units, we will add dollars to them as we work through the remaining steps.
2. Step two is converting the partially completed units into fully completed equivalent units.
We do this for both direct materials and conversion costs.
Often, but not always, materials are added at the beginning of a process.
Whereas conversion costs tend to happen evenly throughout the process.
In this example, let's assume that direct materials have been added at the beginning and the ending WIP is 50% complete for conversion costs.
So here's the math: completed and transferred out ,we had 620 units which are 100% complete for direct materials and 100% complete for conversion costs.
I hope you understand why they are 100% complete, if they'd been completed and transferred from this process they are done with material, labor, and overhead from this process.
Ending WIP has 180 units which are 100% complete for direct materials, meaning we're not adding any more materials to this process, and 50% complete for conversion costs.
Thus, the equivalent units for direct materials is 180 units, but the equivalent units of conversion cost is only 90 units. The total equivalent units is 800 for direct materials and 710 for conversion costs.
So again, you can see where we got those calculated in step two.
3. Step three is similar to step one.
Here we are summarizing the total production cost to account for.
The beginning units of WIP have direct materials and conversion costs already assigned to them.
The new units started have direct materials and conversion costs attached as well.
And recall that conversion costs are direct labor and manufacturing overhead, so I broke these costs down at the bottom of this slide.
As you've learned from prior video, product costs are normally classified as direct material, direct labor, and manufacturing overhead.
If you see a homework problem where you're given labor and overhead separately, you'll need to add them together, to arrive at the conversion costs.
So we can look at our progress thus far with the WIP T account.
We've added the cost to account for. So the total cost transferred out plus costs remaining in ending WIP inventory needs to total 87,815, which is the total of the two production costs amounts listed there.
4. Step four is calculating the cost of direct materials and conversion costs per equivalent unit.
This step is pretty straightforward.
We take the direct material and conversion costs from the prior step and divide them by the total equivalent units calculated in step two.
The total equivalent units is 800 for direct materials and 710 for conversion costs. That's what we're gonna use in step four.
5. Step five is assignment of direct materials and conversion costs to the units completed and transferred out
and to the units of ending inventory.
I've condensed a few of the steps on this slide so you can see all the information needed in this step.
In order to calculate direct materials and conversion costs for the 620 units completed, we multiplied a 620 equivalent units of DM and conversion costs
as calculated in step two, by the cost per equivalent unit of direct materials and conversion costs, calculated in step four.
So we get $42,470 of direct materials and $28,830 of conversion costs which give us a total cost of 71,300.
We do the same thing for the units in ending inventory.
We multiply the 180 equivalent units of direct material by the cost per equivalent unit of direct material for a total of 12,330.
Then we multiply the ninety equivalent units of conversion costs by the cost per equivalent unit of conversion cost for a total of $4185.
This gives us a total production cost of $16,515 for the 180 partially completed units in ending WIP inventory.
So one final look at the WIP T account with these numbers included.
This T account balances because the $87,815 of production costs that need to be accounted for.
$71,300 was transferred out to the next process with the completed units.
$16,515 remain in WIP with the partially completed units as ending inventory.
And if this happened to be our only process or our last process, then be completed and transferred out would be called cost of goods manufactured and transferred to finished goods inventory, rather than the next work in process account.
And that concludes the five steps of process costing.